Redacción Canal Abierto | El primer colectivo propulsado por un motor eléctrico recorre las calles de la ciudad de La Plata. Silencioso y amigable con el medio ambiente, ya que no produce emanaciones de dióxido de carbono, el vehículo de la Empresa Nueve de Julio S.A.T. comenzará en breve a transitar la ciudad de las diagonales como parte del recorrido universitario, que conecta las distintas facultades de la Universidad Nacional de La Plata (UNLP).
La iniciativa del primer bus de este tipo desarrollado en el país se hizo realidad gracias a la alianza estratégica entre esta casa de estudios y la empresa de transporte público. El vehículo, aportado por la empresa, originalmente tenía un motor convencional y fue reconvertido tras 18 meses de trabajo y ensayos en uno de propulsión eléctrica con baterías de litio con una autonomía de 200 kilómetros. El costo de este desarrollo fue de 250 mil dólares, valor que implica la mitad de lo que costaría importar una unidad lista para circular.
La Facultad de Ingeniería de la UNLP estuvo al frente de este proyecto financiado por el Ministerio de Ciencia y Técnica de la Nación (MinCyT) a través de un Aporte no Reembolsable Asociativo de la Agencia Nacional de Promoción de la Investigación, el Desarrollo Tecnológico y la Innovación.
La reconversión
En las instalaciones del Centro Tecnológico Aeroespacial de la Facultad de Ingeniería (UNLP) se llevaron adelante los trabajos para la reconversión del micro. Del proyecto participaron los ingenieros Alejandro Patanella (aeronáutico), quien condujo el equipo, Guillermo Garaventa (electrónico), responsable de las baterías, y Bautista Nebbia (electromecánico). También aportaron su trabajo los estudiantes de Ingeniería Electromecánica Javier Eguren, Juan Pablo Ane, Juan Ignacio Cuenca y Francisco Tiberi, y el estudiante de Ingeniería Electrónica Alejandro Epifanio.
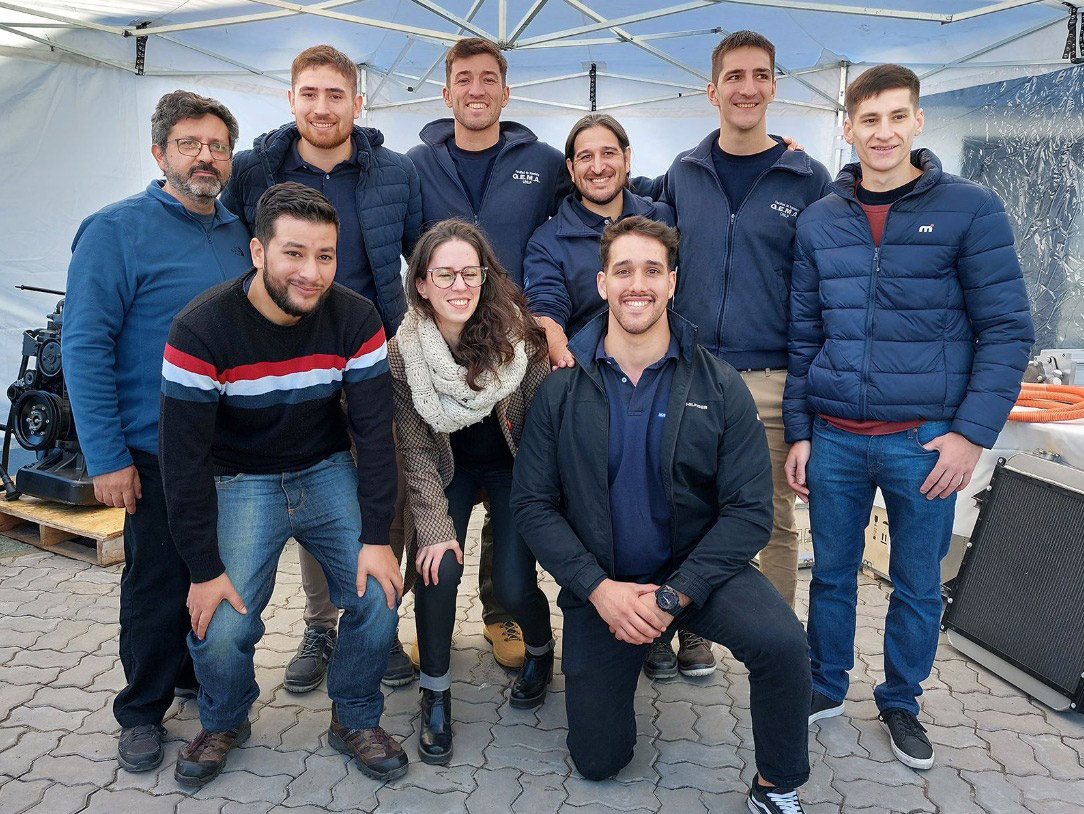
“Venimos hace rato trabajando con este tema que consideramos un punto de partida para empezar a hacer transporte sustentable para las grandes ciudades”, explica Patanella en diálogo con Canal Abierto, responsable de coordinar el equipo de trabajo. “En la época de pandemia tuvimos la idea y tomamos contacto con la gente de la empresa Nueve de Julio, responsable de siete líneas de colectivo en La Plata. Al directorio y al presidente de la empresa, Walter Mastropietro, les gustó mucho la idea y pusieron un micro 0 Km a disposición. Nosotros pusimos la gente capacitada, el laboratorio y un montón de cosas, que quizás no eran las mejores, pero con las que pudimos empezar a mover el tema”.
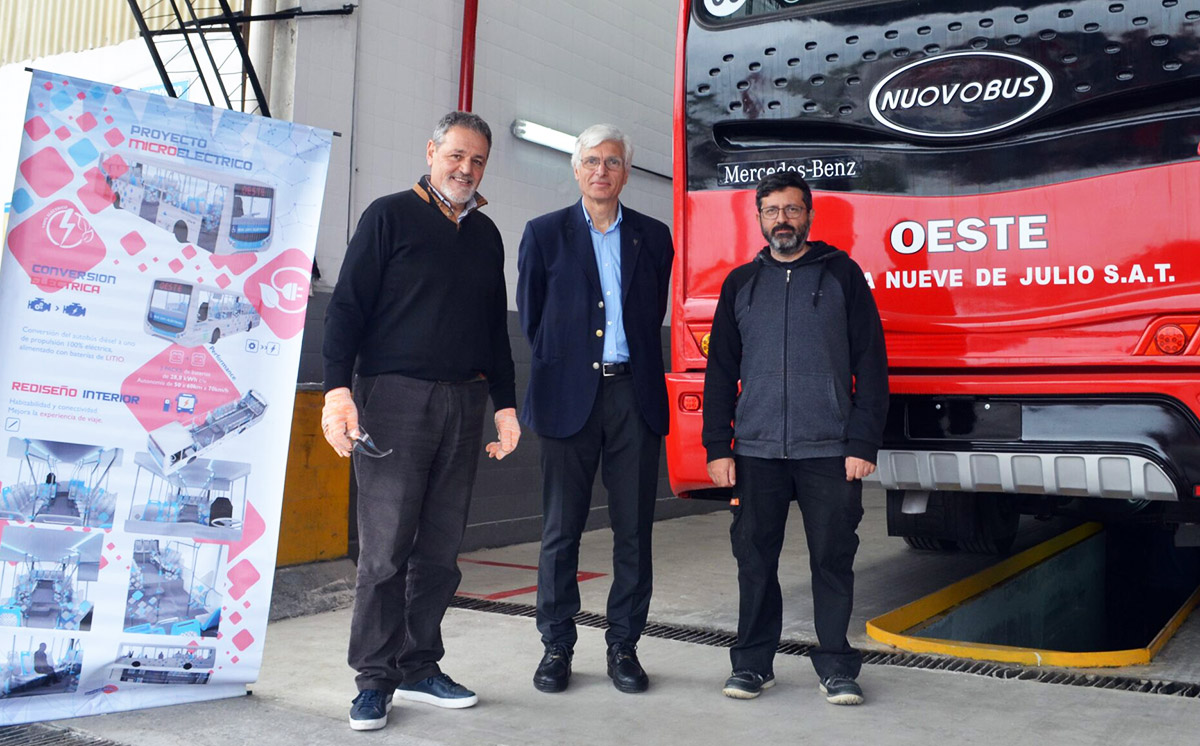
Así, durante la pandemia el equipo de la UNLP comenzó a diseñar un demostrador tecnológico –un prototipo– y construyó un vehículo que tenía unos 50 a 60 kilómetros de autonomía. “Al tiempo, salió una convocatoria del MinCyT para emprendimientos verdes y presentamos un proyecto para la reconversión de este bus. Con ese subsidio pudimos comprar mejor equipamiento, accesorios y baterías con mayor capacidad como para poder armar un vehículo que pueda prestar servicio diario. Buscamos que la autonomía media se adecuara al recorrido promedio de la compañía que era de alrededor de 200 kilómetros”, explica el ingeniero aeronáutico.
Técnicamente, la reconversión consistió en sacar todo el motor diesel, el motor estándar, con su caja de marchas, el sistema de refrigeración, la dirección hidráulica y los compresores de aire comprimido. Se sacó el tanque de nafta, el tanque de brea, el escape y todo lo asociado al motor a combustión. Eso se reemplazó por un motor eléctrico que se acopló directamente al cardan, derecho al diferencial, y se incorporó una batería con ocho paquetes de celdas montadas debajo del piso del ómnibus, entre el chasis y el faldón. Las celdas se montaron simétricas y distribuidas entre los dos ejes para que el peso quedara repartido.
“Básicamente se cambio un motor por otro y lo que sería el tanque de combustible en este caso son las baterías. En el desarrollo participó el personal del taller de la empresa, gente muy proactiva, con mucha energía, con muchas ganas. En el grupo hay alumnos, investigadores y profesionales de varias carreras y áreas de investigación y pudimos hacer una sinergia muy buena”.
El vehículo tiene una autonomía de un poco más de 200 kilómetros; necesita cuatro horas para cargar las celdas y tiene una velocidad limitada en 60 kilómetros, pero puede llegar a una máxima de 90 kilómetros por hora. A fines de la recarga de electricidad la empresa Edelap instaló en la terminal una estación de carga.
Las bondades del colectivo eléctrico
“Uno de los problemas más grandes que tienen los choferes es el ruido del motor que a veces les provoca sordera del oído derecho, debido a que la mayoría de las unidades tienen el motor al lado del chofer. Además, las vibraciones que absorben durante la jornada laboral en el cuerpo les pueden generar trastornos, como el hormigueo en las manos”, explica Patanella.
“Pudimos comprobar que la cantidad de vibración que absorbe el chofer se redujo sustancialmente y que el ruido dentro del vehículo también. Podés hablar como estamos hablando ahora, sin levantar la voz. Desde el punto de vista del peatón, si estás parado en una esquina y pasa un micro como el nuestro por delante tuyo, el ruido es el del ambiente, medimos una variación de no más de 2 a 3 decibeles más que el ruido ambiente. Si lo comparamos con un vehículo diésel estándar, tendrían que pasar seis vehículos eléctricos iguales a este simultáneamente para equiparar el nivel de ruido”.
De acuerdo a las mediciones realizadas sobre el nivel del ruido en el coche eléctrico se registraron 66 decibeles en promedio, que es considerado como el ruido ambiente, mientras que en un coche a combustión se llega a los 87 decibeles, valores que resultan perjudiciales para el ser humano.
“Una de las veces que salimos a probar el micro, dentro de la terminal estaban haciendo un cambio de turno y los invitamos a los choferes, que nunca se habían subido, a hacer un recorrido. Había un chofer que está por jubilarse este año; se subió y no hizo muchos comentarios pero, al final, se le quejó a la gente de la empresa diciendo: ‘¿Hacen esto ahora que me estoy jubilando?’”.
El vehículo en cuestión ya fue probado en la ciudad y sólo falta cumplimentar los últimos detalles con la CNRT y la instalación de la máquina lectora de tarjeta SUBE para que comience a circular regularmente por calles y diagonales.
Beneficios económicos
Las ventajas ambientales y para la salud de trabajadores y pasajeros no son las únicas bondades de esta iniciativa. “La empresa está consumiendo con los vehículos diesel casi medio litro por kilómetro de gasoil. Deben utilizar el diesel que cumple la norma Euro V, el gasoil premium, cuyo precio ronda los 280 a 300 pesos. Con esos valores están gastando alrededor de 140 pesos de gasoil por kilómetro. Con el motor eléctrico estarían gastando 17 pesos el kilómetro. A eso tenés que sumarle el ahorro en aceite, filtros y correas que el micro eléctrico no utiliza”, describe Patanella.
Según los cálculos del equipo de la UNLP, luego de un año y medio a dos años de operación, a razón de 100.000 kilómetros por año, se amortiza el costo de la instalación del motor eléctrico. Luego de ese plazo, al motor le quedan seis años de vida más por delante, lo que arroja que con 8 años de vida de un micro eléctrico estás ahorrando entre un 87% a un 85% del costo que tendrías con un micro diesel.
“Decimos 8 años porque las celdas que utilizamos te aseguran un mínimo de 3.000 cargas sin perder prestaciones. Pero no significa que cumplido el tiempo no sirve más, sino que paulatinamente va perdiendo autonomía. No es que la tengo que tirar, es como el celular que cada vez te dura menos”, explica el ingeniero.
La unidad reconvertida utiliza 168 celdas de litio de hierro fosfato importadas que “tienen que viajar juntas el resto de su vida útil”, no pueden reemplazarse individualmente. En un futuro este proyecto busca utilizar las celdas que en breve comenzará a producir en el país UniLib, la planta que la UNLP e YTEC tienen en esta misma ciudad.
Un primer paso
“Entre otras razones, nosotros decidimos impulsar esta iniciativa porque permite utilizar mucha mano de obra intensiva, de todas las profesiones, y de todos los niveles de educación. Vos vas a cualquier terminal, operadora o taller de este tipo, como la empresa 9 de Julio, y tiene la capacidad para armar y desarmar la carrocería, el motor, la transmisión, todo ese conocimiento está. Tenés desde un chapista hasta un mecánico, algún ingeniero, algún diseñador industrial capaz, tenés todo un abanico. Se puede empezar a capacitar a la gente, concientizándola y empezar un camino que te lleve, de acá a cinco o seis años, a tener una producción 100% nacional o maximizando la producción nacional”, explica el ingeniero un objetivo a largo plazo de este proyecto.
El equipo de la UNLP también está trabajando con la empresa JEMSE (Jujuy Energía y Minería Sociedad del Estado) en Jujuy para transferir el conocimiento para montar allí un centro de reconversión. Su intención es ir replicando la experiencia en distintos puntos del país, idealmente uno en cada provincia y tres o cuatro en la zona del AMBA.
Este proyecto permite generar trabajo y tecnología propia, sin tener que comprar en el exterior lo que podemos desarrollar en el país. “Acá hay mucha capacidad para hacerlo, hay cosas en que no tiene sentido competir porque estamos muy atrás en la carrera tecnológica, pero en este área podemos darle trabajo a mucha gente”.
“Para nosotros, como universidad, nuestra función es desarrollar la tecnología y transferirla en beneficio de la sociedad en general. Vamos en ese camino. Nosotros tenemos proyectos de satélites, hacemos ensayos de seguridad de butacas de auto para niños, de implantes de distinto tipo para el cuerpo humano… esta reconversión fue otra faceta”.
“Me parece importante destacar la alegría de los trabajadores, parecía una fiesta de cumpleaños, la gente de taller y los choferes estaban todos muy contentos, saben que este cambio viene y que les mejora la calidad de vida a los conductores”, concluye Alejandro Patanella.
[mks_toggle title=»UniLiB: baterías de litio industria nacional» state=»open»]UniLiB es un emprendimiento entre la UNLP e YTEC (YPF Tecnología). Se trata de la primera Planta Nacional de Desarrollo Tecnológico de Celdas y Baterías de Litio y se ubica en el Polo Productivo Tecnológico “Jorge Alberto Sábato” que la universidad platense posee en diagonal 113 entre 64 y 65.
Luego de dos años de desarrollo prevén que entre agosto y septiembre de este año iniciarán la producción de celdas nacionales para la fabricación de baterías de ion-litio destinadas a abastecer de energía a viviendas y a vehículos de gran porte como colectivos. [/mks_toggle]
Fotos: Prensa UNLP